Bearing shell seat hole is an important part of generator set crankshaf. If it is damaged, generator set will not work normally. Today Starlight shares the methods to repair bearing shell seat hole.
How to repair bearing shell seat hole of crankshaft of generator set?
When repairing the damaged and worn bearing shell seat hole, it is often used to pad another copper sheet behind the upper and lower bearing tile to adjust the expansion. Then the method of adding boring and scraping volume to the bearing tile is adopted.
This method has certain effect on the bearing shell seat hole of low speed engine with uniform wear. However, the effect is not good for diesel engine if seat hole is wear and out of round, and the wear amount is more than 0.10 mm.
If directly brush plating the worn seat hole, it can not guarantee the uniform coating; if thermal spray repair welding is adopted, the cylinder block will be heated and easily deformed; because of the large hole spacing, complex shape, difficult positioning, high requirements and small processing amount, it is not easy to ensure the coaxiality of the main bearing shell seat hole of the cylinder block when it is processed by boring machine after spraying; when there is no boring equipment, the machining is more difficult.
In the process of using engine of diesel generator set, there are often accidents of burning and holding the bearing due to various reasons. In the engine with high speed and heavy load, once the bearing accident occurs, the consequences are serious.
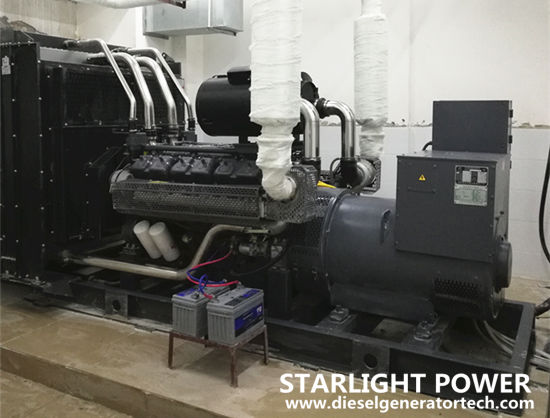
For example, the wear of some engine crankshaft seat hole is 0.3-0.5mm, which can not be repaired according to the traditional method. But after exploring and summing up the experience and lessons, we finally found an effective way to solve this kind of problem, that is, to repair it with boring method. The specific method is as follows:
First, identify whether the worn cylinder block bore has repair value or not. If has, we can plate copper by brush plating method( other coatings can be used, but they must be strong enough and suitable for processing), brush the wear hole to the original size and leave a machining allowance of about 0.15mm.
If you find the above problems in the process of using diesel generator set, you must repair the unit in time. If you can't solve it by yourself, you must find a professional technician to deal with it. Hope the above information can help you.
Here we also share the causes of bearing shell damage in diesel generators.
The damage types of the bearing shell of diesel generators mainly are eccentric wear, scratch (damage), embedded foreign matter, wear, peeling off, burning and melting, fatigue, cavitation, chemical corrosion, etc., and the direct causes are as follows:
1.Oil shortage, oil cut-off.
2.Low oil pressure.
3.Wrong oil grade, poor oil.
4.Dirty engine oil, water in engine oil, diesel oil in engine oil; mixed use of engine oil.
5.The oil filter is blocked and the filter element is not authentic.
6.Lubricating system pipeline blocked, oil pump failed.
7.The fit clearance is abnormal; the bearing bush is seriously worn, the clearance is increased, the oil pressure is reduced, causing the bush burning, or the clearance is too small.
8.Deformation of main shaft hole and crankshaft.
9.There is a problem with the main bearing shell.
10.Diesel engine overload.
We should pay attention to above reasons to prevent bearing shell damage.
Repair of crankshaft axle suspension bus in generator set.
The repair of this fault is more complicated than that of other faults. Because after axle suspension bus occurs, it will cause deformation of relevant parts. At the same time, a large number of metal particles will be produced due to the axle suspension bus, which will affect the cleanliness of the diesel engine. Therefore, in order to repair the diesel engine, the following work must be done selectively according to the actual situation of the diesel engine:
1.First of all, the relevant parts should be measured: the coaxiality of the crankshaft, the cylindricity of the shaft diameter, the cylindricity of the main shaft hole of the engine body, the cylindricity of the big end hole of the connecting rod, and if they are out of tolerance, must be replaced.
2.Ensure the cleanliness of diesel engine. Because a large number of metal particles will be produced to block the primary filter after occurs axle suspension bus , and the oil will go through the bypass valve, so that the metal particles will be distributed in the lubrication system, if not cleaned, the fault will be repeated.
3.Clean the oil pipeline, the engine oil, oil way of oil filter base, oil filter and oil line of crankshaft; Replace the filter, booster element and oil cooler core ( if the oil does not go through the bypass valve, it does not need to be replaced).
4. Ensure that there is no problem in dimensional tolerance of parts and components, the lubrication system can be reassembled only when there is no metal end.
Starlight is a manufacturer of diesel generator set in China, if you are interested, please contact us by sales@dieselgeneratortech.com.
Comments
Post a Comment