The fuel system of diesel generator set has direct injection type and electronic injection type. Starlight Power will introduce the difference between the two engines in this article.
The engine has four strokes in normal operation: intake stroke, compression stroke, combustion stroke, and exhaust stroke. These four strokes work in a continuous cycle, thus generating a source power for the engine. The difference between the working principle of the EFI and the direct injection engine is the difference in the combustion stroke of the engine.
The difference between engine direct injection and electronic injection:
Direct injection in the engine cylinder: The technology of direct injection of fuel into the cylinder and mixing with the intake air is to directly press the diesel into the cylinder of high temperature and high pressure, so that the diesel can spontaneously ignite and push the piston to move, thus achieving the working operation of the engine. Compared with the EFI engine, the direct injection engine consumes more fuel, the noise is loud, the combustion is insufficient, and the exhaust emission pollution is higher.
Engine EFI: The diesel engine that uses electronically controlled fuel injection and emissions is an EFI diesel engine. According to the diesel engine status signal, the electric control calculates the injection quantity and injection timing required for each cylinder of the engine, and injects the diesel fuel into the cylinder for atomization through the injector under a certain pressure. It mixes with the air stream of the intake air and enters the combustion chamber to ensure that the engine and catalytic converter are always working at their best, but parts such as the spark plug need to be replaced more frequently.
Direct injection: daily maintenance cost is low, the engine torque is large, and the power is sufficient. Disadvantages: Poor diesel can be used. The fuel supply causes the carbon accumulation in the cylinder to increase, the power and speed is reduced, and it is not easy to ignite.
EFI (Electronic Fuel Injection): good matching with the hydraulic system, three more high-pressure oil injection than direct injection, stable power generation, the disadvantage is that the diesel oil requirements are high.
Environmental protection: direct injection engine has strong adaptability to oil products, but the fuel can not be completely burned, the oil consumption is large, and it is not environmentally friendly; the electronic injection type has high requirements on oil products, sufficient fuel, low displacement, energy saving and environmental protection.
The direct injection engine is a traditional engine. Its fuel injection to the system depends only on the system pressure generated by the engine working under different working conditions. The fuel supply system performs fuel injection on the engine working under different working conditions according to the working pressure, that is to say, the fuel supply of the direct injection engine depends only on the system pressure, so it is easy to cause the fuel which can not be accurately supplied according to different working conditions, affecting the normal operation and service life of the engine.
However, the modern EFI diesel engine just uses the modern computer control technology to solve the shortcomings of the traditional diesel engine. It makes good use of sensor detection technology (sensor) to detect the working state of the engine under different working conditions, such as pressure, temperature, air intake, etc., and sets the most reasonable working pressure and the fuel needed of the system under different working conditions in advance in the computer. In this way, the computer can monitor various data of engine operation under different working conditions in real time, and accurately supply fuel according to different working conditions, and make the system fuel supply not depend on the system pressure, but depends on the fuel supply time, that is, the engine working conditions determined by the computer based on the monitoring data are connected to the electric pulse of the injector. (In the EFI diesel engine, the injector is not turned on like a traditional pressure, but becomes an electromagnetic type injector. Depending on the electromagnetic force to turn on.) This achieves the effect of fuel economy and noise reduction, and also prolongs its service life.
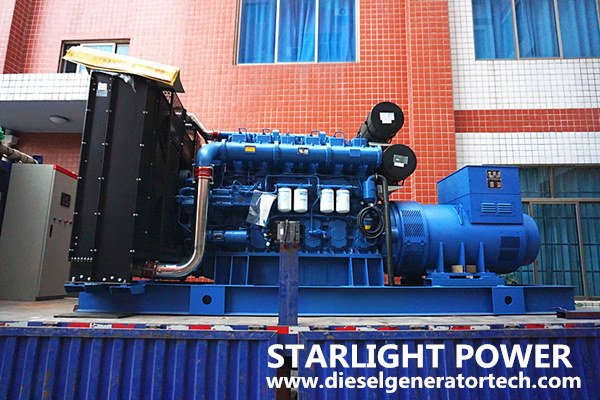
Customers will choose different types of fuel injection engines according to their actual needs. There are many ways of engine fuel electric injection. The most common one is the electronically controlled high pressure common rail technology.
The electronically controlled high pressure common rail technology is a very mature technology used in the current engine. The fuel injection system is mainly composed of sensor, high pressure common rail pipe, electronically controlled fuel injector, high pressure oil pump and ECU. The fuel pressure generation and fuel injection are divided into two parts. The engine speed does not directly affect the pressure in the high pressure common rail pipe. The action of the high pressure oil pump keeps the fuel in the high pressure common rail pipeline at a stable high pressure condition.
Fuel injection principle
The sensor can collect the speed, load and other parameters of the engine. After these parameters are analyzed by ECU, the pressure in the common rail pipe is adjusted to achieve accurate control of oil pressure. At the same time, the injection time and fuel injection amount are adjusted by the solenoid valve on the injector controlled by ECU to maintain the full combustion of the fuel and the efficient operation of the engine.
Structure
The structure of the electronically controlled high-pressure common rail engine is relatively complicated, and the fuel injection is controlled by a complicated circuit, the price is slightly higher, the unit price of each part is higher, and the cost of the later maintenance is relatively high. At the same time, due to the need to accurately control the fuel injection quantity, the electronically controlled high pressure common rail engine has higher requirements on the quality of the fuel oil, and the use of poor quality fuel easily damages the engine.
Why do customers prefer direct injection diesel generator set?
Mainly because the direct injection engine structure is simpler than the electronically controlled high pressure common rail engine, and the failure rate is low, which can maintain a relatively stable fuel consumption. The electronically controlled high pressure common rail engine has high fuel injection precision and low fuel consumption during normal operation. With the increase of time and the increase of the frequency of use, the high pressure oil pump will wear out, the precision of the injector solenoid valve will also decrease, resulting in the oil pressure drop in the high pressure common rail, the injection accuracy is reduced, and the engine of fuel conversion efficiency is decreased. If the engine equipped with the electronically controlled high pressure common rail system is not repaired in time, the fuel consumption will even exceed that of the direct injection engine of the same power.
Comments
Post a Comment