For diesel generator sets, it is important to maintain regularly to ensure the safe operation of the equipment; it is an effective means to restore the technical performance of the equipment, eliminate faults and hidden troubles, and extend the service life of the equipment.
But during the maintenance process, maybe we do not know whether we can maintain properly. So today Starlight Power summarizes some problems in maintenance methods.
1.Failed to check the fitting clearance of parts
In the maintenance of common diesel generator, the clearance between piston and cylinder liner, piston ring "three clearances", piston top clearance, valve clearance, piston clearance, brake shoe clearance, master-slave gear engagement clearance, bearing axial and radial clearance, valve stem and valve guide fitting clearance, etc. There are strict requirements for all types of generating sets. During maintenance, we must carry out measurement, adjust or replace parts that do not meet the clearance requirements.
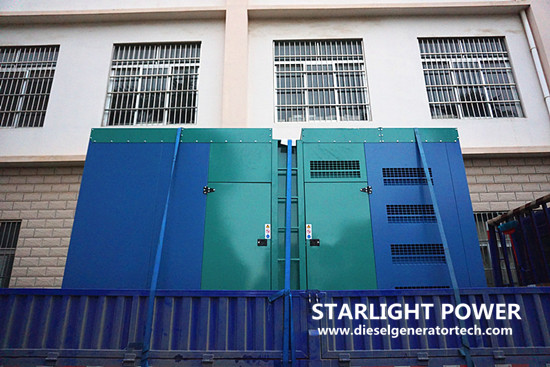
In the actual maintenance operations, if we do not measure the fit clearance, while blindly assemble parts, it will lead to early wear or ablation of bearings, burning of engine oil in diesel generators, difficult starting or deflagration, breaking of piston rings, collision of parts, oil leakage, air leakage and other faults.
Sometimes, it will even lead to serious mechanical damage accidents due to improper fitting clearance of parts.
2.When power generators is assembled, install parts by error
In the maintenance of power generators, some parts assembly has strict direction requirements. Only the correct installation can ensure the normal operation of parts and components. However, in the actual operation, the reverse installation often occurs, resulting in early damage of parts, abnormal operation of machinery, equipment damage accidents, etc. Such as engine cylinder liner, unequal valve spring, engine piston, piston ring, fan blade etc. These parts are easily installed by error. It will cause abnormal operation after assembly, leading to equipment failure.
Therefore, when assembling the parts, the maintenance personnel must master the structure and installation direction requirements of the parts, and can not be assumed to install blindly.
3.Failure judgment and analysis
Because the maintenance personnel are not clear about the mechanical structure and principle of the equipment, do not carefully analyze the cause of the fault, cannot accurately judge the fault location, and blindly dismantle the equipment with the idea of "probably, almost". Results not only the original fault was not eliminated, but also new problems appeared.
When the generator set breaks down, it should be tested by testing equipment. If there is no testing equipment, we can use traditional fault judgment methods, for example "ask, look, check and test" can be used to determine the most likely fault location in combination with the structure and working principle of the equipment. When judging the equipment failure, the common "elimination method" and "comparison method" are from simple to complex, from appearance to interior, from assembly to component.
4.Replace parts blindly
It is relatively difficult to judge and remove equipment faults. Some maintenance personnel always use the method of replacement test. No matter large or small parts, as long as they think that they may be the parts that cause the faults, they will replace one by one to test. As a result, not only the fault was not eliminated, but also the parts that should not be replaced were replaced at will, which increased the maintenance cost. Some faulty parts can be restored to their technical performance through repair, such as generator, air compressor, blower, burner, gear oil pump and so on. They can be repaired without complex repair process.
During the maintenance, the causes and parts of the faults shall be carefully analyzed and judged according to the fault phenomenon. For the parts that can be repaired, the repair method shall be adopted to restore the technical performance, and the blind replacement of parts shall be avoided.
5.Parts are not thoroughly cleaned and decontaminated, and early damage and corrosion often occur.
During the maintenance of equipment, it is of great significance to remove the oil and impurities on the surface of parts to improve the quality of repair and prolong the service life of machinery. Failure to pay attention to the cleaning of parts, improper selection of cleaning agent, improper cleaning methods, etc., will lead to early wear and corrosive damage of parts. If the sundries in the bolt hole and the sand particles in the hydraulic components are not completely removed, the bolt will be damaged.
Jiangsu Starlight Electricity Equipments Co.,Ltd. is a manufacturer of power & generating sets in Jiangsu China, our factory was set up in 1974, we have focused on high quality product for more than 43 years, all product has approved by ISO and CE. Welcome to contact us by sales@dieselgeneratortech.com.
Comments
Post a Comment