Failure of the fuel injection pump of a diesel generator set can easily lead to the problems in the operation of the diesel engine. It is necessary to pay attention to the maintenance when the diesel engine is not working, so that the wear of the fuel injection pump plunger or sleeve can be found in time.
The wear of the plunger and the sleeve is mainly caused by the effect of impurities in the diesel and the high-pressure diesel scour. The common wear parts are the middle part of the top and the spiral edge and the inlet and outlet holes of the sleeve. The surface is dark after wear.
The specific causes of wear of the plunger and sleeve are as follows:
1. The diesel is not filtered nor precipitated, so that diesel contains more impurities.
2. The diesel filter cannot filter. It should be replaced with a new one.
3. The diesel brand is not selected properly. For example, when the temperature is high, diesel with too low viscosity is used to make the plunger and sleeve poorly lubricated.
4. The fuel injection nozzle or fuel outlet valve is stuck in the closed position. In this way, when the fuel injection pressure of the injector is too high, the plunger continues to pump oil, causing the plunger top to be damaged.
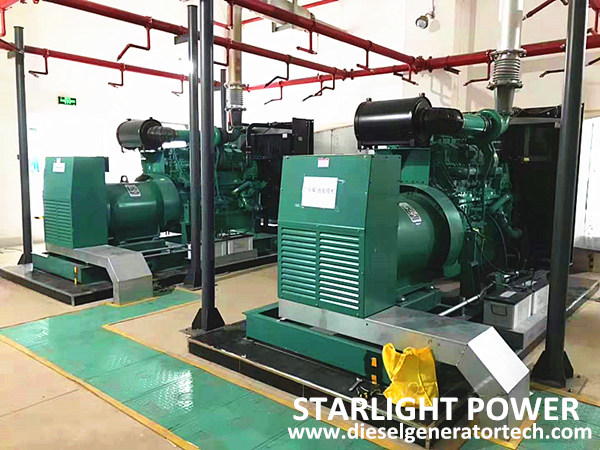
After the plunger and the sleeve are worn, the oil hole of the sleeve is not tightly closed when the oil is pressed, and part of the diesel oil will be pushed back to the oil channel from the worn groove, reducing the oil supply pressure and the oil supply, delaying the start time of oil supply, and the cut-off time is too early, which eventually leads to poor injection atomization. Diesel engines often emit smoke during no-load operation or low load, are easy to turn off at idle speed, and even the injection nozzle needle valve cannot be opened due to the low fuel supply pressure, which cannot be started, and it is easy to make the nozzle carbon accumulation and adhesive phenomenon.
Due to the wear of the plunger and the sleeve, the oil leaks back, which reduces the fuel supply. Especially when the diesel engine runs at idle speed, due to the long oil leakage time and the large amount of oil leakage, the speed of the diesel engine decreases. At this time, the role of the fuel injection pump governor increases the amount of oil and the speed. At this time, the oil leakage decreases again, and the speed of the diesel engine increases. The governor reduces the amount of oil, the speed of the diesel engine decreases, the oil leakage increases again, and the speed of the diesel engine decreases again, the governor increases the speed of the diesel generator, which leads to the high and low speed of the diesel engine.
There are two ways to check the wear of the plunger and sleeve:
1. Adjust the fuel injection pressure of the fuel injector to 200kgf / cm2, and connect it to a group of plunger parts to be inspected. Use the screwdriver to pry the spring seat of the fuel injection pump, the pump oil action is done, or use a starter to drive the diesel engine. If the injector does not inject fuel, the plunger and barrel assembly is worn and needs to be replaced.
2. For the split fuel injection pump, first place the speed regulating fuel supply handle on the fuel supply position, and then pump the fuel with the handle pump. If the fuel sprayed by the fuel injection pump cannot hit the cylinder head, it is indicated that the plunger and sleeve are worn. For the combined fuel injection pump, first place the speed regulating fuel supply handle on the fuel supply position, and then tap the plunger spring with a screwdriver to check the fuel injection of the fuel injection pump.
The Role of Plunger - The plunger is mainly used to convey fluid in a pump or compressor.
The plunger is assembled in a long cylinder block, which can be moved back and forth (push-pull). There are two inlet and outlet pipes equipped with valves, which connect to the cylinder block. The gap between the plunger and the cylinder block is equipped with a suitable seal.
When the plunger moves backward, the outlet pipe valve is closed and the inlet pipe valve is opened, and fluid is sucked into the cylinder from the inlet pipe. When the plunger is moved forward, the inlet pipe valve is closed and the outlet pipe valve is opened. The fluid in the cylinder body is sent out from the outlet pipe, the plunger reciprocates in the cylinder, and the fluid is continuously delivered to the target mechanism. This is the role of the plunger.
Generally, plunger is mainly used in places with high working pressure, and other mechanisms are often used in places with low pressure.
Comments
Post a Comment